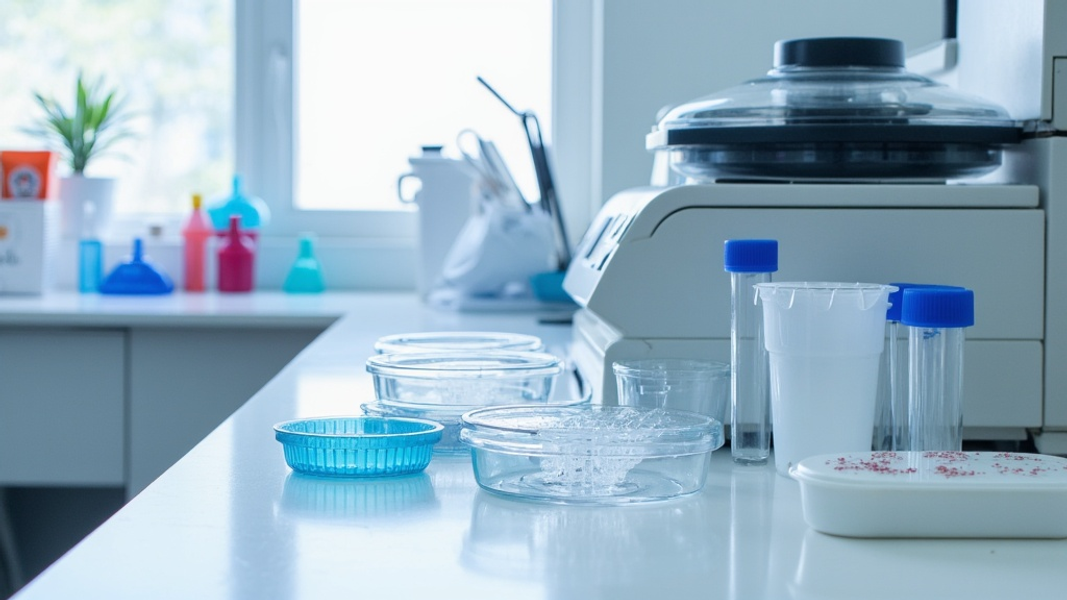
Validation isn't just a checkbox—it's the backbone of quality assurance that can make or break your product's success. This article will provide actionable tips to streamline your validation process, ensuring higher quality outcomes and regulatory compliance.
Understanding the Validation Process
Validation is a crucial step in product development and manufacturing. It ensures that a product meets its specifications and is fit for its intended use. This process is vital for regulatory compliance and managing risks associated with product quality and safety.
Definition and Importance
At its core, validation is about proving that a process, system, or method consistently produces a result or product meeting predetermined specifications. It's not just about testing the final product, but about verifying that every step of the production process is controlled and reliable.
The importance of validation cannot be overstated. It helps companies:
- Meet regulatory requirements
- Reduce product defects and recalls
- Improve customer satisfaction
- Lower production costs by identifying issues early
Types of Validation
There are several types of validation, each focusing on a different aspect of the production process:
Process Validation: This involves checking that a manufacturing process can consistently produce a product that meets its quality attributes. It's about ensuring the repeatability and reliability of the production method.
Equipment Validation: This focuses on proving that the equipment used in production performs as intended. It involves testing and documenting that machines and tools work correctly and consistently.
Cleaning Validation: This is crucial in industries like pharmaceuticals and food production. It verifies that cleaning procedures effectively remove residues from previous production runs, preventing cross-contamination.
Key Stages in Validation
Validation typically involves three main stages:
-
Installation Qualification (IQ): This stage verifies that equipment is installed correctly and meets design specifications. It includes checking things like power supply, calibration, and safety features.
-
Operational Qualification (OQ): Here, we test if the equipment or system works as intended under normal operating conditions. This might involve running the equipment without materials to check its functions.
-
Performance Qualification (PQ): This final stage tests the equipment or process under real-world conditions. It proves that the system can consistently produce the desired results in actual production settings.
8 Essential Tips for an Effective Validation Process
Implementing an effective validation process can seem daunting, but these tips will help you navigate the complexities with confidence.
1. Start with a Comprehensive Validation Plan
A solid validation plan is the foundation of a successful validation process. This plan should clearly define the scope of validation, set clear objectives, and establish acceptance criteria. It's like a roadmap that guides your entire validation journey.
Your validation plan should include:
- A detailed timeline of activities
- Roles and responsibilities of team members
- Resources needed for each stage
- Methods for data collection and analysis
- Criteria for success at each stage
Remember, a well-crafted plan saves time and resources in the long run by preventing confusion and reducing the need for rework.
2. Implement Risk-Based Approach
Not all aspects of a process or product carry the same level of risk. A risk-based approach to validation focuses resources where they're needed most.
Start by identifying critical process parameters (CPPs) and critical quality attributes (CQAs). These are the factors that have the most significant impact on product quality. For example, in pharmaceutical manufacturing, the active ingredient's purity would be a CQA, while the mixing speed might be a CPP.
Once you've identified these critical factors, design your validation studies to test them thoroughly. This approach ensures you're not wasting time and resources on less important aspects while giving proper attention to crucial elements.
3. Establish Clear Documentation Practices
Good documentation is the backbone of validation. It provides evidence that your processes are under control and meet specifications. Clear, detailed records also make it easier to troubleshoot issues and demonstrate compliance to regulators.
Create standardized templates for different types of validation documents. This might include:
- Validation protocols
- Test results forms
- Equipment logs
- Training records
Ensure all documents are easily traceable and include version control. This means each document should have a unique identifier, date, and author. When changes are made, keep a clear record of what was changed, when, and why.
4. Leverage Technology for Data Integrity
In today's digital age, leveraging technology can significantly improve your validation process. Electronic systems can help maintain data integrity, improve efficiency, and reduce human error.
Consider using validated electronic systems for data collection and management. These systems should have built-in audit trails that track who made changes to data and when. They should also have robust security measures to prevent unauthorized access or data tampering.
5. Train Personnel Effectively
Even the best-designed validation process can fail if the people carrying it out aren't properly trained. Develop comprehensive training programs for all personnel involved in validation activities.
Training should cover:
- The principles of validation
- Specific procedures relevant to each role
- How to use any equipment or software involved
- The importance of following protocols exactly
Regularly assess the competency of your team. This could involve practical tests, written exams, or on-the-job observations. Remember, as processes or regulations change, your training programs should be updated too.
6. Conduct Thorough Equipment Qualification
Equipment qualification is a critical part of the validation process. It ensures that all equipment used in production or testing is fit for purpose and performs consistently.
For each piece of critical equipment, conduct IQ, OQ, and PQ as discussed earlier. This might involve:
- Checking that the equipment is installed according to manufacturer specifications
- Testing all functions of the equipment under normal operating conditions
- Running the equipment with actual product to ensure it performs as expected
Don't forget about ongoing maintenance. Establish regular calibration schedules and preventive maintenance routines to keep equipment in top condition.
7. Design Robust Sampling Plans
Sampling is often a necessary part of validation, especially in industries where testing every unit isn't feasible. However, your sampling plan needs to be statistically sound to provide meaningful results.
Use statistical methods to determine appropriate sample sizes. This ensures your results are representative of the whole batch or process. Consider factors like:
- The size of your production runs
- The level of confidence you need in your results
- The acceptable margin of error
Also, think about worst-case scenarios. Your sampling plan should be designed to catch potential issues even under the most challenging conditions.
8. Implement Continuous Monitoring and Review
Validation isn't a one-time event. It's an ongoing process that requires continuous monitoring and periodic review.
Establish key performance indicators (KPIs) for your validated processes. These might include things like:
- Product quality metrics
- Process efficiency measures
- Error or deviation rates
Regularly review these KPIs to ensure your processes are performing as expected. If you notice any trends or issues, investigate and take corrective action promptly.
Also, plan for periodic re-validation. This is especially important if you make any changes to your process, equipment, or materials. Even without changes, it's good practice to re-validate at set intervals to ensure your processes are still performing optimally.
Common Pitfalls to Avoid
While following best practices is crucial, it's equally important to be aware of common mistakes that can derail your validation efforts.
Inadequate Planning
One of the biggest pitfalls in validation is rushing into the process without proper planning. This often happens when there's pressure to get a product to market quickly. However, skipping or shortcutting the planning phase can lead to costly mistakes and delays later on.
Take the time to develop a comprehensive validation plan before you start. This includes defining your validation strategy, identifying resource needs, and setting realistic timelines. Remember, good planning upfront can save you time and headaches down the road.
Overlooking Change Management
Change is inevitable in any production environment. New equipment, updated regulations, or process improvements can all necessitate changes. However, failing to properly manage these changes can invalidate your previous validation efforts.
Implement a robust change management system. This should include:
- A process for assessing the impact of proposed changes
- Procedures for implementing changes in a controlled manner
- Re-validation protocols for affected processes or equipment
Every change, no matter how small it might seem, should be evaluated for its potential impact on validated processes.
Neglecting Supplier Validation
In today's complex supply chains, many companies rely on external suppliers for raw materials, components, or even entire production processes. However, the quality of your final product depends on the quality of these inputs.
Don't neglect supplier validation. This means:
- Assessing potential suppliers' quality systems
- Conducting audits of critical suppliers
- Establishing specifications for supplied materials or services
- Regularly reviewing supplier performance
Remember, regulatory bodies will hold you responsible for the quality of your product, regardless of where issues originate in the supply chain.
Case Study: Successful Validation at XYZ Pharma
Let's look at how these principles play out in the real world with a case study from XYZ Pharma, a mid-sized pharmaceutical company.
XYZ Pharma faced a significant challenge when they decided to build a new multi-product facility. They needed to validate multiple production lines for different products, each with its own set of regulatory requirements. The complexity of the project threatened to stretch their validation timeline to over a year, potentially delaying product launches and impacting the company's bottom line.
To tackle this challenge, XYZ Pharma implemented a risk-based approach to validation, supported by digital tools. Here's what they did:
-
They used risk assessment tools to identify the most critical processes and parameters for each product line.
-
Based on this assessment, they developed targeted validation protocols, focusing resources on high-risk areas.
-
They implemented an electronic quality management system to streamline documentation and data management.
-
They used simulation software to model processes before physical implementation, identifying potential issues early.
The results were impressive. XYZ Pharma completed the validation of their new facility in just 9 months, a 30% reduction from their initial timeline. Moreover, the focused approach led to more robust validation outcomes, improving their compliance position.
Future Trends in Validation
The field of validation is evolving rapidly, driven by technological advancements and changing regulatory landscapes. Here are some trends to watch:
AI and Machine Learning: These technologies are starting to play a role in predictive validation. By analyzing vast amounts of historical data, AI can help identify potential issues before they occur, allowing for proactive validation strategies.
Continuous Validation: Traditional periodic validation is giving way to more continuous approaches. This involves ongoing monitoring and adjustment of processes, supported by real-time data analytics.
Data Integrity and Cybersecurity: As more validation processes move to digital platforms, ensuring data integrity and protecting against cyber threats is becoming increasingly important. Expect to see more focus on blockchain and other secure data technologies in validation processes.
Conclusion
A well-executed validation process is key to ensuring product quality and regulatory compliance. By following these tips and staying aware of common pitfalls, you can streamline your validation efforts and improve outcomes. Remember, validation is not a one-time event but an ongoing process of ensuring quality and consistency. Stay informed about emerging trends and be ready to adapt your validation strategies as technologies and regulations evolve.
FAQ
What is the difference between verification and validation?
Verification checks if a product, service, or system meets specified requirements. Validation ensures it meets the needs of the end-user or customer. Verification asks, "Are we building the product right?" while validation asks, "Are we building the right product?"
How often should we re-validate our processes?
The frequency of re-validation depends on various factors including regulatory requirements, the nature of your product, and the stability of your processes. Generally, you should re-validate:
- After any significant changes to the process, equipment, or materials
- If you notice any trends in your monitoring data that suggest process drift
- At regular intervals as defined by your quality management system, typically annually or bi-annually
What are some common validation documents?
Common validation documents include:
- Validation Master Plan (VMP)
- User Requirement Specifications (URS)
- Functional Requirement Specifications (FRS)
- Design Qualification (DQ)
- Installation Qualification (IQ) protocol and report
- Operational Qualification (OQ) protocol and report
- Performance Qualification (PQ) protocol and report
- Validation Summary Report
Each document serves a specific purpose in the validation process and provides evidence of a systematic approach to quality assurance.